一、精軋機(jī)大傾角鼓形齒主軸
帶鋼熱軋精軋機(jī)的主軸根據(jù)聯(lián)軸器形式,主要有十字萬(wàn)向軸式和鼓形齒式兩種,十字萬(wàn)向軸式的主軸能夠適應(yīng)更大的主軸傾角,鼓形齒聯(lián)軸器能夠傳遞更大扭矩,且使用壽命長(zhǎng)、維修成本低,但主軸的工作傾角超過(guò) 2°,鼓形齒接軸的承載能力將大幅度下降。這限制了鼓形齒接軸在大工作傾角度條件下的應(yīng)用。隨著軋制鋼種的不斷升級(jí),對(duì)軋制力和主軸傾角同時(shí)提出了更高要求,為了適應(yīng)這一變化趨勢(shì),目前一些國(guó)外主軸制造商已經(jīng)開(kāi)發(fā)出能夠在大傾角工況下使用的鼓形齒聯(lián)軸器,德國(guó)西馬克公司率先研發(fā)了大傾角鼓形接軸( 最大帶載工作傾角為 3. 5° ) ,并成功應(yīng)用于德國(guó) Salzgitter 鋼廠,其 F1 和 F2 機(jī)架主軸的最大帶載工作傾角達(dá)到了 2. 4° 。
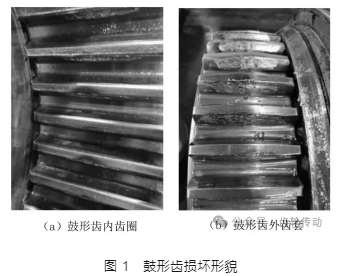
某帶鋼熱連軋精軋機(jī)使用交叉頭控制板型 ,導(dǎo)致主軸扁頭套使用過(guò)程中的位移量和偏轉(zhuǎn)角度變化較大,因此在產(chǎn)線設(shè)計(jì)初期選擇了十字軸式的主軸,出于對(duì)高強(qiáng)鋼、超薄鋼的軋制需求,現(xiàn)場(chǎng)將 F1、F2 兩個(gè)機(jī)架的主軸改為了鼓形齒主軸,采購(gòu)進(jìn)口件 。進(jìn)口鼓形齒對(duì)詳細(xì)的齒形信息保密且價(jià)格較為昂貴,導(dǎo)致鼓形齒維護(hù)工作困難、成本高,為了縮短采購(gòu)周期、降低使用成本 ,某熱軋廠進(jìn)行了鼓形齒國(guó)產(chǎn)化試制,請(qǐng)國(guó)內(nèi)重型機(jī)械制造廠家測(cè)繪了進(jìn)口扁頭套的主要尺寸和鼓形齒內(nèi)齒齒形,以此為依據(jù)制作了備件,但上機(jī)使用數(shù)小時(shí)后發(fā)現(xiàn)鼓形齒處的溫度異常高,隨即緊急停機(jī)更換了主軸 ,異常發(fā)熱的國(guó)產(chǎn)化扁頭套經(jīng)過(guò)解體發(fā)現(xiàn),扁頭套的鼓形齒內(nèi)齒位置有明顯的發(fā)黑碳化痕跡,說(shuō)明停機(jī)前溫度極高,如圖 1a) 所示 ,鼓形齒外齒則能夠看 到明顯的磨損和膠合痕跡 ,如圖 1b) 所示。
為了分析鼓形齒損壞的根本原因 ,尋找國(guó)產(chǎn)件與進(jìn)口件的差別,本文首先設(shè)計(jì)了一套未知參數(shù)齒形和精度的測(cè)量方法,并測(cè)量對(duì)比了國(guó)產(chǎn)和進(jìn)口鼓形齒的齒形和精度,隨后引申討論了鼓形齒的后期修復(fù)問(wèn)題,探討了激光堆焊修復(fù)過(guò)程引起的鼓形齒內(nèi)齒圈變形問(wèn)題,解析了修復(fù)引起內(nèi)齒圈變形的原因,提出了修復(fù)過(guò)程的變形控制方法 ,并在實(shí)際應(yīng)用中驗(yàn)證了該方法的可行性。
二、鼓形齒齒形參數(shù)及精度檢測(cè)
分別測(cè)量了國(guó)產(chǎn)鼓形齒內(nèi)齒套和進(jìn)口鼓形齒內(nèi)齒套的齒形參數(shù)及加工精度 ,以分析國(guó)內(nèi)外鼓形齒在設(shè)計(jì)理念和制造精度兩方面的差異。測(cè)量工作借助齒輪測(cè)量中心進(jìn)行,國(guó)產(chǎn)鼓形齒以測(cè)繪圖紙上的參數(shù)為準(zhǔn),主要包括模數(shù)、壓力角、直徑等,如表 1 所示 ,并以該參數(shù)為基準(zhǔn)測(cè)量齒的制造精度;進(jìn)口鼓形齒未提供具體齒形參數(shù),通過(guò)反復(fù)測(cè)量及擬合修正獲得最為接近的齒形參數(shù),過(guò)程如下:首先試用齒輪測(cè)量中心測(cè)量主要齒形參數(shù),隨后根據(jù)得到的結(jié)果,在不改變基圓的情況下,修正模數(shù)和壓力角的小數(shù)部分,得到數(shù)值較為合理的齒形參數(shù),認(rèn)為是設(shè)計(jì)參數(shù);將修正后的齒形設(shè)計(jì)參數(shù)輸入齒輪測(cè)量中心,再次檢測(cè)進(jìn)口鼓形齒,從而獲得現(xiàn)有齒形參數(shù)和制造精度。
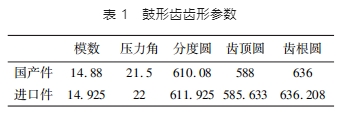
經(jīng)過(guò)測(cè)量,進(jìn)口件的齒形參數(shù)與國(guó)產(chǎn)鼓形齒存在明顯差別,主要體現(xiàn)在模數(shù)和壓力角上,進(jìn)口件的模數(shù)和壓力角的取值均大于國(guó)產(chǎn)件,尤其是壓力角的差異會(huì)導(dǎo)致齒面受力區(qū)域和應(yīng)力值的變化,導(dǎo)致油膜難以建立進(jìn)而引發(fā)本次燒損事故。進(jìn)一步的,測(cè)量了兩種鼓形齒的制造精度,主要測(cè)量齒形、齒向精度和周累精度 。齒形精度測(cè)量結(jié)果如圖 2(a) (b) 所示 , 國(guó)產(chǎn)鼓形齒的齒形精度為 10 級(jí)(國(guó)產(chǎn)鼓形齒測(cè)繪圖紙上要求制造精度達(dá)到 6 級(jí)),進(jìn)口鼓形齒的齒形精度為 4 級(jí);齒向精度測(cè)量結(jié)果如圖 2(c) (d) 所示 , 國(guó)產(chǎn)件為 9 級(jí) ,進(jìn)口件為 4 級(jí);周累誤差測(cè)量結(jié)果如圖 2(e) (f) 所示,周累精度為 9 級(jí),周累精度為 6 級(jí)。從測(cè)量結(jié)果可知,國(guó)產(chǎn)的制造精度均低于圖紙要求的 6 級(jí),也顯著低于進(jìn)口的制造精度 ,根據(jù)各類軋機(jī)上鼓形齒主軸的使用經(jīng)驗(yàn),制造精度差同樣會(huì)引起鼓形齒的異常磨損甚至燒損。進(jìn)口鼓形齒的制造精度在 4 ~ 6 級(jí)之間,因此其圖紙要求的精度應(yīng)當(dāng)為齒形和齒向精度 4 級(jí),周累精度 6 級(jí),略高于國(guó)產(chǎn)圖紙要求。
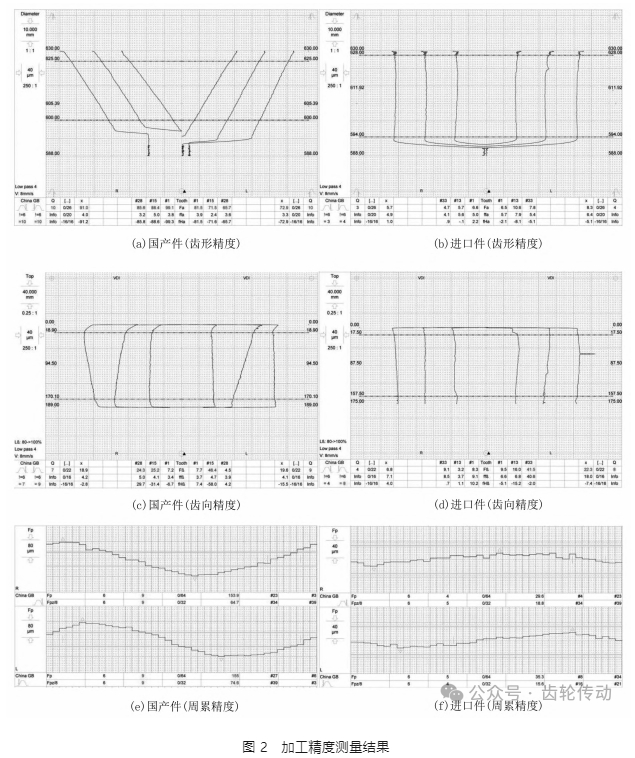
三、扁頭套修復(fù)引起的鼓形齒變形及控制方法
扁頭套修復(fù)工藝及變形量化
扁頭套的扁勢(shì)面在傳動(dòng)時(shí)主要承受正壓力,換輥時(shí)主要承受切向摩擦力,長(zhǎng)時(shí)間使用后發(fā)生顯著磨損需要通過(guò)堆焊恢復(fù)尺寸,并恢復(fù)表面硬度。某熱軋廠常用的修復(fù)手段為激光堆焊,過(guò)程為:首先機(jī)加工去除扁勢(shì)面疲勞層,然后使用激光堆焊恢復(fù)尺寸,最后機(jī)加工至圖紙尺寸,并對(duì)表面進(jìn)行滲碳淬火處理恢復(fù)硬度。扁勢(shì)面滲碳淬火層的厚度≥2mm,硬度要求為 HRC57- 62,因此在去除疲勞層時(shí),難以直接使用機(jī)床加工,通常需要先入爐進(jìn)行消應(yīng)力退火處理,降低表面硬度、改善加工性能。在消應(yīng)力退火的實(shí)操過(guò)程中觀察到,扁頭套及鼓形齒處積累的殘余應(yīng)力釋放,引起結(jié)構(gòu)發(fā)生橢圓變形,尤其是壁厚最薄的鼓形齒處,橢圓趨勢(shì)最為明顯。
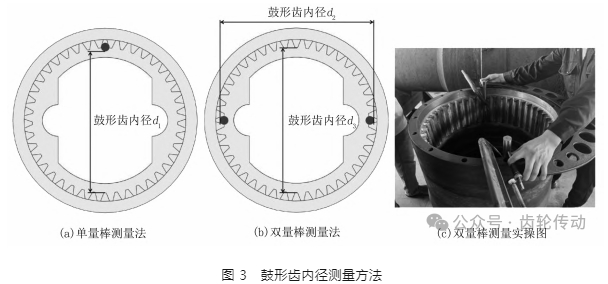
為了定量測(cè)量鼓形齒內(nèi)齒圈的變形程度,設(shè)計(jì)了如圖 3 所示的測(cè)量工裝。選擇兩根直徑為 20mm 左右的金屬棒材,分別放置在第 n 和 n+20 個(gè)齒間隙內(nèi),隨后使用夾鉗將棒材緊緊地固定在鼓形齒齒面上,此時(shí)使用卡尺測(cè)量?jī)蓚€(gè)棒材外徑間距,并不斷調(diào)整卡尺方位,直至測(cè)量到最大的外徑間距,根據(jù)奇數(shù)齒和偶數(shù)齒可以選擇多種不同的測(cè)量方案,圖3(a) (b) 共提供了三種不同的測(cè)量方案,圖 3(c) 為測(cè)量鼓形齒內(nèi)徑 d2 時(shí)的實(shí)操圖。選擇以上任意一種測(cè)量方案,并在每個(gè)界面上測(cè)量四個(gè)不同角度的內(nèi)徑,分別測(cè)量 0°,45°,90°,135°的鼓形齒內(nèi)徑,如圖 4(a) 所示,通過(guò)比較四個(gè)內(nèi)徑的數(shù)值差距可以得到鼓形齒內(nèi)齒橢圓變形的程度,另外為了反映不同壁厚度處的變形程度,分別選擇了三個(gè)測(cè)量截面如圖 4(b)所示 。為了使測(cè)量結(jié)果具有橫向?qū)Ρ纫饬x,需要保證多次測(cè)量選擇相同尺寸的金屬棒材和相同的測(cè)量方案,最后計(jì)算得到不同角度的內(nèi)徑最大差值進(jìn)行變形量大小的對(duì)比,差值越大說(shuō)明內(nèi)齒圈變形越大。
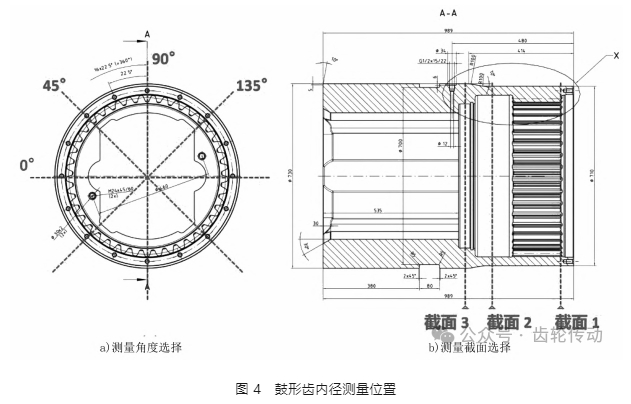
根據(jù)該方法 ,實(shí)測(cè)了一套下機(jī)修復(fù)的扁頭套截面 1 位置的鼓形齒內(nèi)徑 ,分別測(cè)量了下機(jī)后、消應(yīng)力退火、堆焊及滲碳淬火后的變形量,并測(cè)量了一個(gè)鼓形齒新品尺寸做對(duì)比,結(jié)果如表 2 所示。對(duì)比各個(gè)階段的最大差值可以看出,使用一個(gè)周期后,鼓形齒的變形量不明顯,兩次熱處理帶來(lái)的熱變形較為顯著,消應(yīng)力退火后的直徑最大差值增大了 0. 43mm,堆焊和滲碳淬火后的直徑最大差值增大了 0. 94mm,參考齒形測(cè)量結(jié)果 ,鼓形齒對(duì)齒形和精度要求較高,如此變形量將嚴(yán)重影響再次上機(jī)使用。
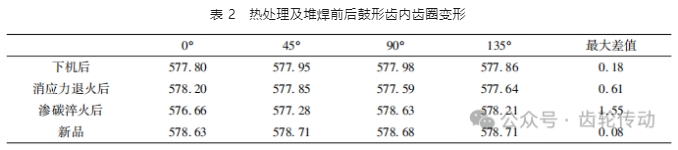
扁頭套變形控制方法
1. 抱箍熱處理法
加工一個(gè)具有一定厚度和高度的圓桶形抱箍,如圖 5 (a) 所示,抱箍與鼓形齒外徑之間采用過(guò)盈配合,通過(guò)加熱漲大后安裝到鼓形齒外側(cè)。使用過(guò)盈配合主要有兩個(gè)目的:其一 ,能夠施加收緊的預(yù)緊力,達(dá)到增大鼓形齒處壁厚、防止熱處理中發(fā)生變形的效果;其二,抱箍平均直徑大于鼓形齒內(nèi)齒圈,在加熱溫度相同時(shí),抱箍的漲大量略大于鼓形齒內(nèi)齒圈,需要通過(guò)預(yù)制過(guò)盈量保證抱箍始終與鼓形齒貼合。
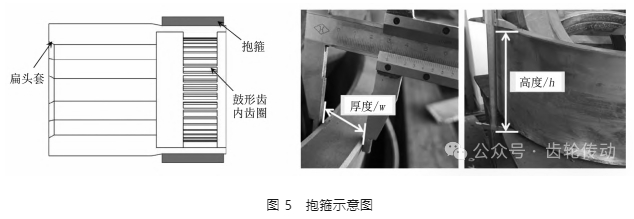
為了達(dá)到減小或防止熱處理變形的目的,抱箍設(shè)計(jì)時(shí)需要考量三個(gè)主要的尺寸參數(shù):
1) 抱箍厚度:圖 5(b) 為抱箍厚度的定義及測(cè)量方法,厚度主要影響抱箍施加的抱緊力的大小,壁厚需要大于扁勢(shì)面厚度與鼓形齒內(nèi)齒圈厚度的差值,使得安裝抱箍后的鼓形齒內(nèi)齒圈總壁厚大于扁勢(shì)面處厚度。
2) 抱箍高度:圖 5( c) 為抱箍高度的定義及測(cè)量方法,抱箍需要覆蓋鼓形齒端絕大部分的薄壁結(jié)構(gòu),主要指圖 4(b)中的截面 1 和截面 2,并且抱箍應(yīng)當(dāng)延伸至超過(guò)扁頭套的位置,以保證抱箍能夠在壁厚較厚的扁頭套處獲得足夠的軸向抗彎能力,否則抱箍易跟隨鼓形齒端整體發(fā)生偏斜。
3) 過(guò)盈量:過(guò)盈量指抱箍與鼓形齒之間的配合過(guò)盈量,選值需要考慮消應(yīng)力退火、堆焊、滲碳戰(zhàn)火過(guò)程抱箍的溫升,保證受熱膨脹后抱箍和鼓形齒外側(cè)始終貼合,基于此原則可以得到最小過(guò)盈量 δ 的計(jì)算公式為 :

式中:
α—鋼材的線膨脹系數(shù) ,可以近似為 10-5/ ℃;
Db —抱箍外徑;
Dg —和鼓形齒外徑;
Ta —最高溫度溫度;
T0 —室溫;
w—抱箍厚度;
b—余量系數(shù) ,根據(jù)實(shí)際情況在 1. 1 ~ 1. 3 之間取值。
抱箍過(guò)盈量不易取得過(guò)大,需要考慮抱箍裝拆的便捷性。
現(xiàn)場(chǎng)實(shí)際使用抱箍進(jìn)行消應(yīng)力退火的鼓形齒內(nèi)齒圈變形如表 3 所示。
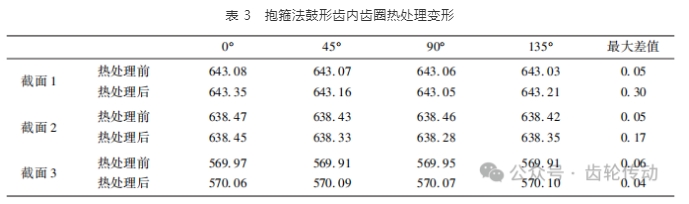
通過(guò)比較四個(gè)相位內(nèi)徑的差值,可以看到內(nèi)齒圈任存在橢圓變形趨勢(shì),但是相較不使用抱箍時(shí)具有明顯減小,截面 1 熱處理前的最大差值為 0. 05mm,熱處理后為 0. 3mm,增大量為 0. 25mm (不使用抱箍時(shí)的增大量為 0. 43mm) 減小了 41. 8% 。
截面 2 熱處理前的最大差值為 0. 05mm,熱處理后為 0. 17mm;截面 3 熱處理前的最大差值為 0. 06mm,熱處理后為 0. 04mm。截面 1 和截面 2 的位置發(fā)生了顯著的橢圓變形,截面 3 基本未發(fā)生變形,對(duì)比發(fā)現(xiàn)壁厚越薄,橢圓變形越明顯,截面 1 位于鼓形齒處,該處壁厚最薄,變形量最大。
2. 鼓形齒冷矯法
對(duì)于已經(jīng)發(fā)生變形的鼓形齒內(nèi)齒圈,可以使用冷矯的方法。首先使用量棒測(cè)量各角度的直徑,找到直徑最大的位置,直徑最小處通常與該位置呈 90°夾角,使用夾具在直徑最大的位置由外向內(nèi)夾緊鼓形齒,同時(shí)使用千斤頂和頂桿在直徑最小的位置由內(nèi)向外撐緊鼓形齒,并保持一定時(shí)間 ,隨后重新檢查各個(gè)相位的直徑大小,找到最大、最小直徑并利用上述方法進(jìn)行冷矯,直至變形量達(dá)到期望值。
3. 線切割法
在去除疲勞層時(shí),使用線切割代替機(jī)加工,由于線切割不受材料硬化的影響,因此可以不進(jìn)行消應(yīng)力退火直接去除疲勞層。但是線切割的效率低,完成扁頭套內(nèi)孔疲勞層切割需要花費(fèi)較長(zhǎng)的加工時(shí)間,通常無(wú)法滿足現(xiàn)場(chǎng)的修復(fù)周期要求,且線切割的成本較高,比較適合精度要求高、修復(fù)時(shí)間充裕的場(chǎng)合。
四、結(jié)論
通過(guò)對(duì)進(jìn)口、國(guó)產(chǎn)鼓形齒扁頭套的齒形和精度的測(cè)量,以及對(duì)修復(fù)過(guò)程中的經(jīng)驗(yàn)總結(jié),本文主要得到如下結(jié)論 :
1) 扁頭套的鼓形齒內(nèi)齒圈對(duì)模數(shù)和壓力角較為敏感,國(guó)產(chǎn)件的齒形與進(jìn)口件存在差異,是造成鼓形齒燒損的主要原因;
2) 國(guó)產(chǎn)件的圖紙精度要求為 6 級(jí),實(shí)際加工精度在9 ~ 10 級(jí)之間未達(dá)到圖紙要求,進(jìn)口件的實(shí)際精度為 4 ~ 6 級(jí),高于高產(chǎn)圖紙要求;
3)扁頭套修復(fù)時(shí)進(jìn)行的消應(yīng)力退火導(dǎo)致的變形與壁厚負(fù)相關(guān),壁厚越薄則橢圓形變形越明顯,鼓形齒內(nèi)齒處變形最為明顯,鼓形齒與扁勢(shì)面的過(guò)渡位置幾乎不產(chǎn)生變形;
4) 通過(guò)在熱處理過(guò)程中佩戴抱箍,能夠緩解薄壁處產(chǎn)生的橢圓變形,使用抱箍后鼓形齒處的內(nèi)徑最大差值由 0. 43mm 降低至 0. 25mm,減小了 41. 8% 。
作者簡(jiǎn)介:馬遵農(nóng) ,寶山鋼鐵股份有限公司
參考文獻(xiàn)略.